Organizations embarking on Enterprise Lean Transformations use “Lean Techniques” as vehicles to accomplish specific breakthrough business strategies and objectives. An inflection point in the organization’s collective learning curve occurs when its members become “believers” and gain competence with the basic Lean tools through repeated successful applications. A key component of this enabling competence for transforming an organization is the 5-day Kaizen or rapid improvement event.
Leveraging the skills and experience of our experts, the Lean Enterprise Platform provides the basis to effectively support 3-5 simultaneous teams. The team’s objectives, goals, and deliverables are identified during a preparation process between the LVSI and the Lean core teams. The experts teaches the required tools, guides their application, and coaches and mentors teams and management to accomplish changes necessary to achieve the “future state” vision defined by the initial value stream analysis.
A standard event is 5 days of rapid, focused, team action where the deliverable is a changed, more effective process that yields immediate improvements. Key to the kaizen process is to ensure the work areas are re-configured and fully operational by the week’s end to allow the organization to enjoy the results and gain the return on investment of resources made during the event.
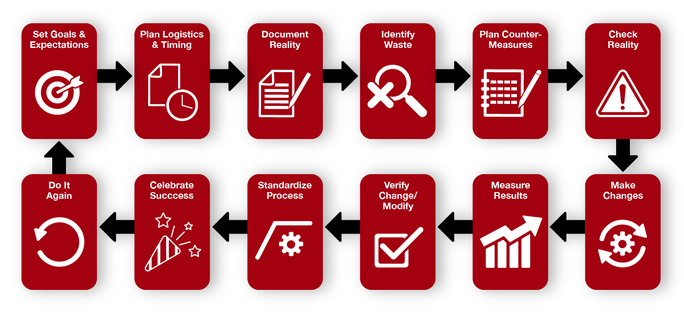
The kaizen daily pace process is summarized as follows:
Day 1 – Study current conditions
The kaizen week begins with an official kick off by senior leadership that defines the teams’ goals and objectives, team makeup, and approach for the week “empowering” teams to implement break-through changes during the kaizen week. The kaizen teams receive an overview of Lean principles and basic Lean tools from the sensei. They validate the current conditions “As-Is” in each event team’s area, identifying wastes inherent in processes and gathering data.
Day 2 – Implement major changes
The kaizen teams begin to make changes that must take place (including equipment moves), and track specific achievable benefits and associated metrics. Teams ensure the work areas are reconfigured and fully operational by the week’s end.
Day 3 – Tryout and debug
The kaizen teams will spend the majority of the day supporting the newly configured work area, assessing progress on moves and key items needed for completion. This is a critical day to ensure significant progress is made in meeting objectives by week’s end.
Day 4 – Standard work and redeploy
The kaizen teams document standard work for “new processes” to ensure procedures are followed by work members. Establishing “standard work” is the heart and soul of the Lean transformation process and ensures that the “normal” condition is established. Also, appropriate staffing levels are put in place with product flowing by days end validating the new process. The teams, along with the leadership, will need to re-deploy employees in certain instances to ensure that the savings are realized.
Day 5 – Presentation of Results and Recognition
The event week culminates with a “Celebration” out brief attended by all the senior leaders and key customers and suppliers. The ultimate deliverable is a changed, more effective process that yields immediate improvements.