Kaizen is Japanese for revolutionary improvement and translates for businesses into the organized use of common sense to improve business operations including cost, quality, delivery and customer service.
The Kaizen methodology promotes sustainable continuous improvement as a daily way of life for every member within the organization, encouraging all members of the organization to propose and implement improvement ideas.
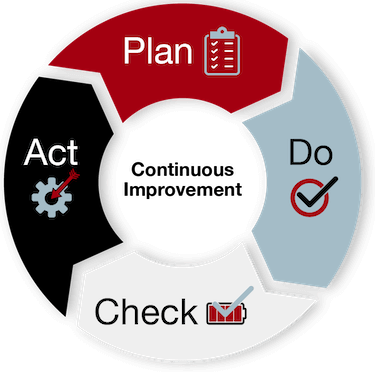
Kaizen Events
A Kaizen event is the use of cross-functional teams to create rapid change for a specific project in a short period of time. Kaizen is best used on projects where a problem is clearly defined and understood and there is an immediate need for results.-
- Standard Work – The most powerful tool within the Toyota Production System Methodology. Learn how to flow work, operators and machines to TAKT time and develop a stable and predictable process.
- Cellular Manufacturing – Understand the concepts and implement the change in your organization from batch processing to 1-piece flow while reducing labor, inventory and increasing quality.
- Set-up Reduction – Take machine set-up times from hours to minutes to seconds! Learn how to combine the resources of the floor, tool room and support groups in identifying waste in set-ups.
- Visual Factory – Increase productivity by making your factory easy for you and your employees to navigate and improve the flow of vital communication to the floor!
- Total Preventive Maintenance (TPM) – A one-week workshop that is comprised of operators, maintenance personnel and supervisors to implement a total productive manufacturing system for increased machine capacity and up-time.
- Quality Control Process Charting – A highly powerful but simple technique used to identify and quantify all those informal rework & reprocessing activities that fly under the radar of standard quality systems.